Пружина сжатия 3D модель
При изготовлении пружин сжатия между их витками обязательно оставляются зазоры: если их не будет, то эти изделия попросту не смогут выполнять свою функцию. При этом их крайние витки всегда поджимают к виткам соседним, а торцевые поверхности обязательно зашлифовывают по плоскостям, которые располагаются строго перпендикулярно продольным осям этих деталей. Благодаря этому обеспечивается как центральное направление сжимающей нагрузки, так и легкость установки пружин на опорных плоскостях. Пружины сжатия большой длины могут терять устойчивость (в технике такой процесс называется «выпучиванием»), и для того чтобы предотвратить это, их часто устанавливают либо на стрежнях, либо в направляющих стаканах.
Наибольшее распространение получили цилиндрические винтовые пружины. Дело в том, что их форма прекрасно соотносится с формой стаканов, валиков и прочих тел вращения. Несколько реже применяются винтовые конические пружины. По сравнению с пружинами цилиндрическими, они более устойчивы, кроме того, в полностью сжатом состоянии их высота минимальна. Их главным недостатком является сложность изготовления. В принципе, конические пружины могут быть сжаты до очень небольших размеров, а именно – до размера, равного той толщине, которую имеет проволока, из которой они навиты: дело в том, что в процессе сжатия их витки входят один в другой с совсем небольшим зазором.
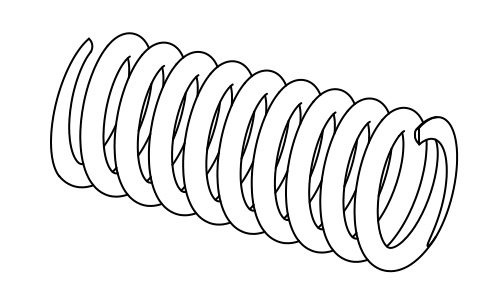
В технике, при разработке различных машин и механизмов, поставленные перед конструкторами задачи часто могут быть решены использованием, как пружин растяжения, так и пружин сжатия. В подавляющем большинстве случаев разработчики отдают предпочтение пружинам сжатия, поскольку их использование подразумевает:
• Упрощение конструкции;
• Отсутствие ограничителей больших деформаций;
• Более высокую надежность конструкции в целом.
Сейчас при проектировании практически всех пружин сжатия активно используются специализированные пакеты прикладного программного обеспечения, которые позволяют на стадии разработки этих деталей создавать их трехмерные модели. Это существенно облегчает работу конструкторов, ускоряет выполнение всех необходимых расчетов, а также делает процесс действительно творческим.
В качестве материала, из которого изготавливаются пружины сжатия, чаще всего применяются специальные стали, имеющие высокую упругость, а также сплавы цветных металлов, которые при сжатии и растяжении с допустимыми расчетными нагрузками способны восстанавливать свою первоначальную форму.
Следует заметить, что выпуск стальной пружинной проволоки является достаточно сложным и трудоемким процессом. Технология предполагает протяжку исходного материала на специализированных волочильных станках, последующую термическую обработку, а также травление, которое осуществляется для формирования необходимого сечения на промежуточных стадиях производства.
Для того чтобы в процессе навивки пружин не возникало вмятин, сколов и каких-либо других дефектов, к поверхности проволоки предъявляются достаточно жесткие требования. Их строгое соблюдение обеспечивает высокую надежность и качество изготавливаемых пружин.
При закалке пружин необходимо строго соблюдать технологический режим. При изготовлении пружин из проволоки, имеющей небольшое сечение, можно не подвергать их последующей термообработке, а использовать уже готовую проволоку. Когда же производятся силовые пружины, которые испытывают на себе значительные нагрузки, то применяется отожженная сталь, а после навивки они подвергаются закалке.
Если при закалке резко охлаждать пружины в воде, то это может привести к появлению так называемых закалочных трещин. Поэтому такую закалку используют редко, а если и применяют, то в воду добавляют различные примеси, чтобы снизить скорость охлаждения. Самыми предпочтительными закалочными средами являются воздух и масло.