Допуск формы заданной поверхности
Отклонение поверхности от его номинального значения характеризует величина допуска заданных форм к действительным геометрическим параметрам. Допуск формы заданной поверхности изображается на поле чертежа в виде выгнутой дуги замкнутой горизонтальной линией и цифровым значением.
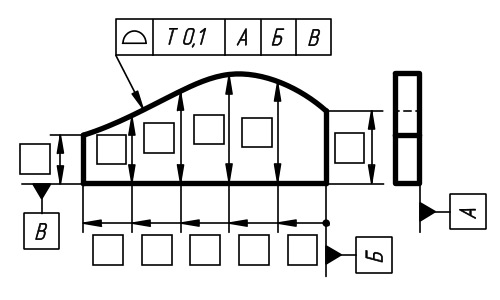
Допуск формы заданной поверхности относительно поверхностей
А, Б, В,
Т 0.1мм
.
Технология литья в кокиль является наиболее качественным методом получения изделий с повышенными требованиями к допускам формы заданной поверхности. Литьём в кокиль получают отливки из чугуна, сталей, алюминиевых, и прочих сплавов. Детали получаемее данной технологией более точны, их внешний вид имеет более, конкурентные, эстетические параметры, а так же за счёт минимальной усадки уменьшают расход материала.
Кокиль это специальная геометрическая форма, выполненная из металла, которая заполняется различными литейными сплавами. По окончании застывания и охлаждения, кокиль раскрывают и извлекают из её полости, готовое изделие. После чего кокиль можно использовать для последующего технологического цикла. При литье в кокиль заполнение рабочего пространства сплавом и его затвердевание происходят под действием силы тяжести земной гравитации.
Особенно эффективно использование кокильного литья при серийном и массовом изготовлении отливок из алюминиевых сплавов и сплавов магния. Такие сплавы имеют относительно небольшую температуру плавления, поэтому один и тот же кокиль можно использовать неоднократно с количеством рабочих циклов около 10000
раз. У сплавов стали, температура плавления достаточно высокая, при получении стальных отливок стойкость кокилей снижается, исходя из чего метод кокильного литья, для стали менее приемлем, чем для цветных сплавов.
Металлическая форма, из которой изготовлен кокиль, по сравнению с другими видами литейных конструкций , обладает значительно большей прочностью, теплопроводностью, теплоемкостью и весьма малой газопроницаемостью. Литьё в кокиль даёт минимальную усадку отливки, что может вызвать затруднения при извлечении готовой детали из формы, однако у этого метода есть ряд приимуществ. Рабочие полости выполняются с достаточно высокими характеристиками по точности, что в свою очередь делает возможным получение готовой продукции с более, конкурентными показателями по точности, которые соответствуют двенадцатому, пятнадцатому квалитетам.
Разброс точности по весу, получаемых отливок при использовании литья в кокиль, достаточно не высокий, что даёт возможность уменьшения размеров необходимых для припуска на последующую технологическую обработку резанием.
Взаимодействие металла, из которого получается отливка и кокилем, в ходе технологического процесса, относительно минимально, за счёт чего шероховатость поверхности соответствует достаточно хорошим показателям, которые обеспечивают как прочностные, так и эстетические требования на должном уровне.
Большая скорость охлаждения расплава отливок в кокиле, вызывает увеличение скорость ее затвердевания, что положительно влияет на структуру, которая становится менее, зернистая, в затвердевающем растворе. Технологические режимы литья выбирают в зависимости от свойства сплава, геометрической конфигурации отливки и предъявляемым требованиям к изделию.
Для воздействия на скорость отвода тепла от различных частей отливки, толщину слоя и свойства огнеупорных покрытий, в разных частях формы кокиля, зачастую делают различными. Поверхности каналов литников, системы подачи расплавленной массы, покрывают более толстым слоем специальных красок с уменьшенной теплопроводностью, а поверхности прибыльных частей в отдельных случаях оклеивают тонким листовым асбестом. Продолжительность времени выдержки отливки в кокиле определяют с учетом ее размеров и общей массы.
Технология литья в кокиль является одним из наиболее широко востребованных способов изготовления изделий в форме отливок. Несмотря на отдельные недостатки, кокильное литьё является одним из производительных методов, используемых в серийном, и массовом производстве.