Подшипник качения
Подшипники, которые в технике используются очень широко, представляют собой опорные кинематические механизмы. Они используются в самых различных агрегатах, машинах и оборудовании для того, чтобы определять взаимоположение их движущихся частей, а также способствовать их эффективному перемещению.
Подшипники играют роль опор вращающихся осей и валов. Кроме того, они воспринимают прикладываемые к ним осевые и радиальные нагрузки, а также транслируют их на корпусные детали машин. Подшипники также обеспечивают надежное фиксирование валов в определенном положении и их вращение вокруг заданных осей.
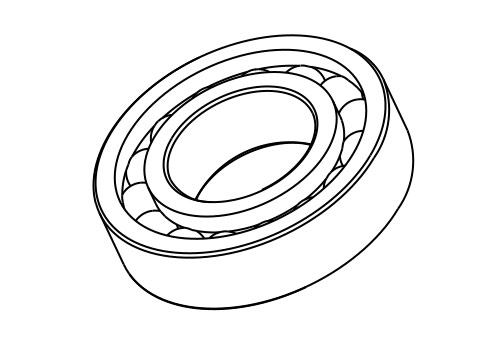
Все современные подшипники качения представляют собой изготавливаемые на специализированных предприятиях большими сериями стандартные изделия. От подшипников скольжения они отличаются гораздо более высоким коэффициентом полезного действия, простотой в обслуживании, существенно меньшими линейными размерами, пониженным теплообразованием и меньшими моментами сил трения. Что касается недостатков, то они у подшипников качения также есть. Таковыми являются довольно значительные размеры диаметров, пониженная способность к демпфированию колебаний и ударов, а также отсутствие диаметральных разъемов.
Сейчас при проектировании подшипников качения разработчиками активно используются пакеты специализированного прикладного программного обеспечения, позволяющие создавать трехмерные модели готовых изделий на стадии их конструирования. Это существенно ускоряет и упрощает разработку, облегчает проведение всех необходимых расчетов, делает процесс проектирования в значительной степени творческим.
В качестве материала изготовления шариковых, игольчатых и роликовых подшипников качения (причем как обычных, так и прецизионных) применяются специализированные подшипниковые стали, соответствующие ГОСТ 801–78
.
К подшипниковым сталям предъявляются достаточно высокие требования. Им надлежит обладать высокой износостойкостью и контактной выносливостью, высоким сопротивлением пластической деформации. Подшипниковые стали должны быть достаточно пластичными при высокой твердости и иметь минимум неметаллических включений.
Согласно действующим нормам и стандартам, для маркировки подшипников используются буквы Х
(«хромистая») и Ш
(«шарикоподшипниковая»), а также числа, которые показывают в десятых долях процента содержание хрома. Наиболее распространенными марками подшипниковых сталей являются ШХ15
, ШХ4
, ШХ9
, а также дополнительно легированные марганцем и кремнием ШХ15СГ
, а также ШХ20СГ
. Следует заметить, что из подшипниковых сталей с высоким содержанием легирующих примесей изготавливаются подшипники с шариками и роликами больших размеров.
Рабочие поверхности деталей подшипников обрабатываются с высокой точностью и высоким качеством, они подвергаются термической обработке. Именно эти факторы и являются определяющими степень надежности и долговечность готовых изделий.
Детали подшипников качения закаливаются при температуре от +790 °С
до +840 °С
, причём чем больше масса детали, там выше температура. Кольца и ролики охлаждают в растворе соды, а шарики – в воде или растворе поваренной соли. Твердость этих деталей подшипников после закаливания составляет HRC62–65
.
То, насколько подшипник качения будет долговечным, во многом зависит от качества изготовления тех деталей, на которые он напрессовывается, а также от качества его установки. Если посадочные места имеют овальность или конусность, то подшипники напрессовываются с перекосом, посадка ослабляется, посадочные места ускоренно изнашиваются. Поэтому оправка должна иметь такую конструкцию, которая обеспечивает посадку подшипника без перекоса, равномерную нагрузку на торец запрессовываемого кольца, а также центрирование.