Допуск круглости
На деталях вращения цилиндрической и конической формы, после обработки по условиям технологического процесса, образуются поверхности с присущими им отклонениями. Чтобы указать вид и степень погрешности, на чертеже наносится специальный знак в виде окружности и цифровое значение.
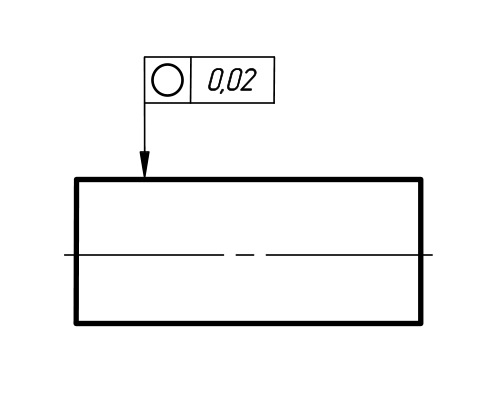
Допуск круглости цилиндрической
поверхности 0.02 мм
.
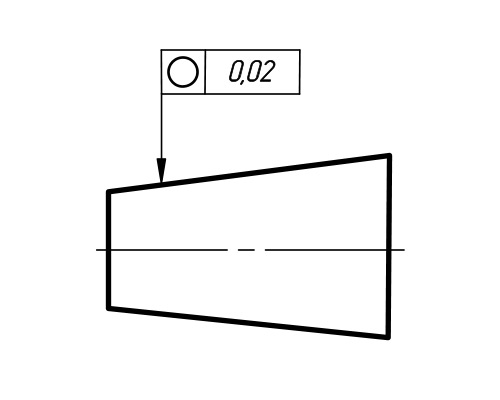
Допуск круглости конической
поверхности 0.02 мм
.
По определению окружность, это кривая на плоскости, все условные точки которой равноудалены, на расстояние радиуса от центральной точки, а диаметр окружности соответственно равен удвоенной величине радиуса.
При механической обработке деталей цилиндрической и конической формы, происходит образование поверхности с определённой шероховатостью, а соответственно и отклонением её формы. Допуск круглости обозначает отклонение кривизны окружности, на участке детали условно пересеченном плоскостью, от номинальной окружности.
Отклонение от круглости, характеризуется такими геометрическими изменениями как овальность и огранка, выражаемой в отклонениях от реального профиля к прилегающей окружности. Такие отклонения получаются в результате механического воздействия на поверхность обрабатываемой детали из-за режимов обработки и качества крепления заготовки.
Контроль круглости осуществляется при помощи специального прибора, называемого кругломером. Этот прибор предназначен для измерения отклонений от округлости в поперечном сечении деталей при их бесцентровом вращении, то есть без использования её оси вращения. Кругломер, может использоваться как в условиях измерения непосредственно в цехе, так и в лабораторных условиях.
Обработка на кругло шлифовальных станках
Круглые цилиндрические детали обрабатываются на специальных, точных станках таких как: кругло-шлифовальные центровые станки, внутришлифовальные станки, бесцентрово-шлифовальные станки, профилешлифовальные станки. Станки этой группы способны выполнять: шлифование круглых и конических наружных поверхностей, шлифование профильных поверхностей, обработку круглых внутренних поверхностей. Выбор метода шлифования определяется типом производства, конструкцией изделия, характером припуска и требованиями к точности исполнения и качеству обработки.
В ходе технологического процесса связанного с удалением слоя материала происходит изменение геометрии детали с определёнными отклонениями её формы и размера. Все операции круглого шлифования можно разделить на три вида обработки: обдирочное, предварительное и тонкое шлифование.
Обдирочное шлифование используют для удаления с заготовок технологического слоя материала с поверхности, после литья, ковки, штамповки, прокатки. Скорость шлифовального круга составляет при этом Vк = 35 – 60 м/с
и более, шероховатость поверхности при данном методе обработки, соответствует Rа=2,5 – 5
микрометров, а точность обработки в интервале от восьмого, до девятого квалитета.
Предварительное шлифование выполняют, как правило, после токарной обработки, но перед термическим воздействием на материал. Режимы предварительной обработки шлифованием производятся при скорости вращения шлифовального круга не менее Vк = 40 – 60 м/с
, точность обработки соответствует шестому, девятому квалитету, при этом шероховатость обрабатываемой поверхности составляет Rа=1,2 – 2,5 мкм
.
Окончательное шлифование выполняют после термической обработки. Скорость круга при финишной обработке составляет Vк = 35 – 40 м/с
и более, где точность обработки соответствует пятому, шестому квалитету, средняя арифметическая величина шероховатости Rа = 0,2 – 1,2
мкм.
Тонкое шлифование применяется, в случае если нужно обеспечить очень малую величину шероховатости поверхности, порядка Rа=0,025 – 0,1
микрометров. Припуск для тонкого шлифования выбирается в интервале от 0,05 мм
до 0,1 мм
на диаметр.